It's Time to discover Tube Swaging (Continued)
Take well points, for example; those rugged metal cones used to penetrate layers of soil, sand, and rock to establish water wells. Diversico produces over 60,000 of these each year by swaging, and the advantages of the process are obvious.
The material is inexpensive black iron pipe and there is no waste. For 2" well casings, the 2-3/8" OD pipe is cut into 4" lengths, which then are swaged to form a 6" long cone having a solid homogenous tip. Swaging work hardens the tip to the point where it can penetrate flagstone without being damaged, and no other hardening or tempering processing is subsequently necessary. Diversico swages these well points for 1" wells also, and supplies both sizes to a number of well equipment manufacturers.
Another swaging application involves the tubular awning poles for a prominent manufacturer of camping trailers. Originally, these poles were tipped with small castings which fitted grommets in the awning to support it when in use. Besides being expensive, these small castings were highly susceptible to breakage and wear.
Diversico's solution to both these problems was to swage the end of the pole itself into a solid, rod-like tip form. The short taper formed by this reduction supports the awning while the straight tip section is small enough to slip easily into the grommet, and long enough to hold it securely.
Besides eliminating the casting and its related assembly costs, the awning pole tip looks better, wears longer because of the work hardening effect of swaging, and is much, much stronger.
While swaging was able to eliminate the cast component in the foregoing example, this is not always possible. Turbine engine temperature probes, for example, require that 321 stainless steel tubes be tightly anchored to Hastelloy "X" castings. In this case however, swaging did prove to be an extremely satisfactory way to join these dissimilar metal components.
Using what Diversico calls an "interrupted swage", a series of square-shaped indentations in two rows on the circumference of the casting were filled with metal displaced by swaging the stainless steel tube over the casting. The result was a tight, strong bond between the two components that was uniformly leakproof and made the assembly capable of withstanding intense vibration and thermal shocks.
Among hundreds of other part design configurations produced by swaging at the Diversico plant are motorcycle muffler shells and exhaust pipes, heat exchanger tubes, and soil probes. The latter are used in turf aerators, and are the little hollow spikes which make the holes and remove the soil cores. Diversico has been making these probes by swaging for more than 45 years; to date no better way has been found to make them.
Other Methods Extend Abilities. While the equipment in Diversico's 20,000 sq ft plant includes Fenn and Abbey Etna rotary swaging machines capable of handling tubes ranging in size from hypodermic needles to 12 in. diameters and lengths to 40 ft, other types of equipment are used to complement the rotary swaging process. These include hydraulic presses, draw benches, and a recently acquired Torrington 323-SS swager in which the spring loaded dies do not rotate, and which can be used to produce Phillips head screw drivers and other such shapes.
The use of this equipment extends the company's ability to form bar and tubing into parts having complex internal and external contours.
Thanks to the application of one of these complementary processes, a manufacturer of small internal combustion engineers will save about $12,000 this year on the cost of approximately 20,000 exhaust manifold headers.
Originally, these headers were swaged to shape from 1" mild steel tubing, then a 3/16" thick mounting flange was assembled to each header and welded in place. Unfortunately, the heat from the welding operation created distortion which resulted in improper fit between header and tapered exhaust port in the aluminum engine at assembly. The resultant leakers were unacceptable.
To solve this problem, Diversico developed a fixture which automatically positions the flange at the proper distance from the end of the exhaust header and holds it while specially designed internal tooling is used in a horizontal hydraulic press to expand the header at the point of flange contact. Besides squeezing the header material tightly against the encompassing flange, the process forms a slight bead on each side of the flange. The result is a stronger, more rigid, and better appearing assembly with no distortion, and a 16-cent saving per header in labor and material costs.
Another example of how Diversico uses these complementary processes and its ability to develop special tooling to produce less expensive, better performing parts is in the production of flow meter venturi. Some of these are used in medical testing equipment for measuring a patient's breathing volume. Others have different purposes and range in size to the flow meters used on large diesel engines.
As shown at right in the accompanying photo, the conventional method of making these venturi involved the joining by welding of four parts; one made by spinning, one by drawing, and the two ends by cutting straight tubing to length. Critical dimensions are the diameter of the restriction, angle of the cone, and the radius between restriction and end diameter. This method is expensive, and since smooth flow of air through the venturi is essential, all welds must be dressed so that no seams appear on the inside.
Seeking to make less expensive, but sturdier and more reliable venturi, Diversico developed tooling and methods capable of producing these complex forms in one piece.
The one-piece venturi at left in the photo is formed form 1-1/8 in. 304 stainless steel tubing. Its interior is seamless and has an extremely smooth surface. Obviously, it is an improvement over the larger welded model shown, and "There is no more economical way to make them," says H. Blaine Fluth, Diversico president.
Somewhat different in configuration are the Pitot tubes Diversico makes for supersonic aircraft. These are formed from nickel tubing with IDs swaged to tolerances as close as plus or minus 0.001 in.
Also pictured on these pages are two small parts which have no useful purpose other than to demonstrate Diverico's ability to form tubing. At the left in this photo is a short length of 3003-H14 aluminum tubing with a half-in. nut permanently secured in its upper end. This assembly is accomplished by electromagnetic pulse forming on a new Magneform machine built by Maxwell Laboratories, Inc. and recently acquired by Diversico to further extend it s tube forming capabilities.
The part at right in this photo has been sawn in half to present a cross sectional view. Made of 1020 steel tubing having wall thickness of 0.049 in., it illustrates what Diversico can accomplish with the DOM (drawn over mandrel) technique. Note the three thicknesses of material at the bottom created by forming two opposed 180-degree bends.
While neither of these are actual production parts, it is hoped their inclusion in this article will encourage other ideas on the use of tube forming for production components. Diversico bases its success on this kind of thinking, and encourages everyone to adopt the "Imagineering" approach.
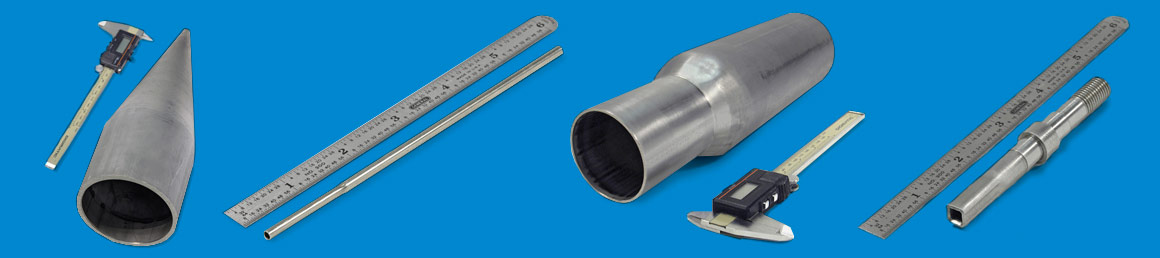